
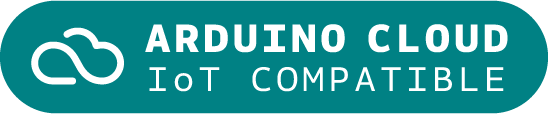
Arduino Opta WiFi
Discover everything our most versatile Opta micro PLC has to offer: designed for engineers who need to keep their options open.
Overview
Arduino Opta is a secure, easy-to-use micro PLC with Industrial IoT capabilities.
Designed in partnership with Finder – leading industrial and building automation device manufacturer – Opta allows professionals to scale up automation projects while leveraging the Arduino ecosystem. Supporting both Arduino sketch and standard PLC languages, including LD (Ladder Logic Diagram) and FBD (Function Block Diagram), it was designed with PLC engineers in mind.
Its powerful STM32H747XI dual-core Cortex®-M7 +M4 MCU allows users to perform real-time control, monitoring and implement predictive maintenance applications.
Secure and durable by design, it supports OTA firmware updates and ensures data security from the hardware to the Cloud thanks to the onboard secure element and X.509 Standard compliance. In addition, Opta undergoes regular assessments to uphold and improve its cybersecurity posture.
All while maintaining Arduino Pro’s signature easy deployment in production thanks to a vast range of readily available software libraries and Arduino sketches.
Last but not least, various connectivity options make keeping everything under control effortless via real-time dashboards combined with the intuitive Arduino Cloud (or third-party services).
Opta comes in three variants so you can choose the best option for your project. Opta WiFi features Ethernet onboard and USB-C programming ports, RS485 half duplex connectivity interface, and Wi-Fi/Bluetooth® Low Energy connectivity.
More than you need? Check out Opta RS485 or Opta Lite.
Program it with the Arduino PLC IDE!
The Arduino PLC IDE makes PLC programming easy. Choose any of the 5 programming languages defined by the IEC 61131-3 standard (Ladder, Functional Block Diagram, Structured Text, Sequential Function Chart or Instruction List) and quickly code PLC applications or port existing ones to Arduino Opta.
Key benefits include:
- Easy and fast software development, starting from ready-to-use Arduino sketches, tutorials and libraries
- Support for standard IEC 61131-3 PLC languages
- Fieldbus integration via Modbus TCP (ethernet) and Modbus RTU (serial RS485)
- Seamless IoT connectivity (Ethernet/Wi-Fi/Bluetooth® Low Energy)
- Real-time remote monitoring via intuitive Arduino Cloud dashboards (or third-party services)
- Security at the hardware level thanks to onboard secure element and X.509 Standard compliance
- Secure OTA firmware updates and Cloud device management
- High-power relay switching (4 x 2.3 kW)
- Reliable by design, thanks to industrial certifications and Finder’s expertise in switching technology
- Easy to install, with DIN rail compatibility
Opt in to industrial automation
Integrate a solid and reliable micro PLC with your existing machines, devices and production lines – also in combination with other elements in the modular and versatile Arduino ecosystem, from small and smart sensor-packed modules to SOMs to gateways, for end-to-end solutions that can be customized to meet any need.
Quality by design
Arduino Pro partnered with Finder, a leader in the field of electromechanical and electronic components with 65+ years of excellence and expertise to its name, to create a product with high-quality production specs for even the most demanding work conditions in industrial environments.
Need Help?
Check the Arduino Forum for questions about the Arduino Language, or how to make your own Projects with Arduino. If you need any help with your product, please get in touch with the official Arduino User Support as explained in our Contact Us page.
Warranty
You can find your product warranty information here.
Tech specs
Input | 8x configurable digital / analog (0-10V) input |
Processor | STM32H747XI Dual ARM® Cortex®:
|
Connectivity | Support 10/100 Ethernet (TCP/IP or Modbus TCP) USB-C Wi-Fi + Bluetooth® Low Energy RS485 half duplex |
Memory | 1MB RAM (programming) 2MB internal + 16MB Flash QSPI |
RTC | Typical 10 days power retention at 25°C NTP sync available through ethernet |
IP protection | IP20 |
Output | 4x relays (250 V AC - 10 A) |
Programming languages |
|
Security | ATECC608B Secure element |
Supply voltage | 12…24 V DC |
Operating Temperature | -20 °C to +50 °C (-4°F to 122°F) |
Certifications | cULus listed, ENEC, CE |
Resources for Safety and Products
Manufacturer Information
The production information includes the address and related details of the product manufacturer.
Arduino S.r.l.
Via Andrea Appiani, 25
Monza, MB, IT, 20900
https://www.arduino.cc/
Responsible Person in the EU
An EU-based economic operator who ensures the product's compliance with the required regulations.
Arduino S.r.l.
Via Andrea Appiani, 25
Monza, MB, IT, 20900
Phone: +39 0113157477
Email: support@arduino.cc
Documentation
Learn more
Get Inspired
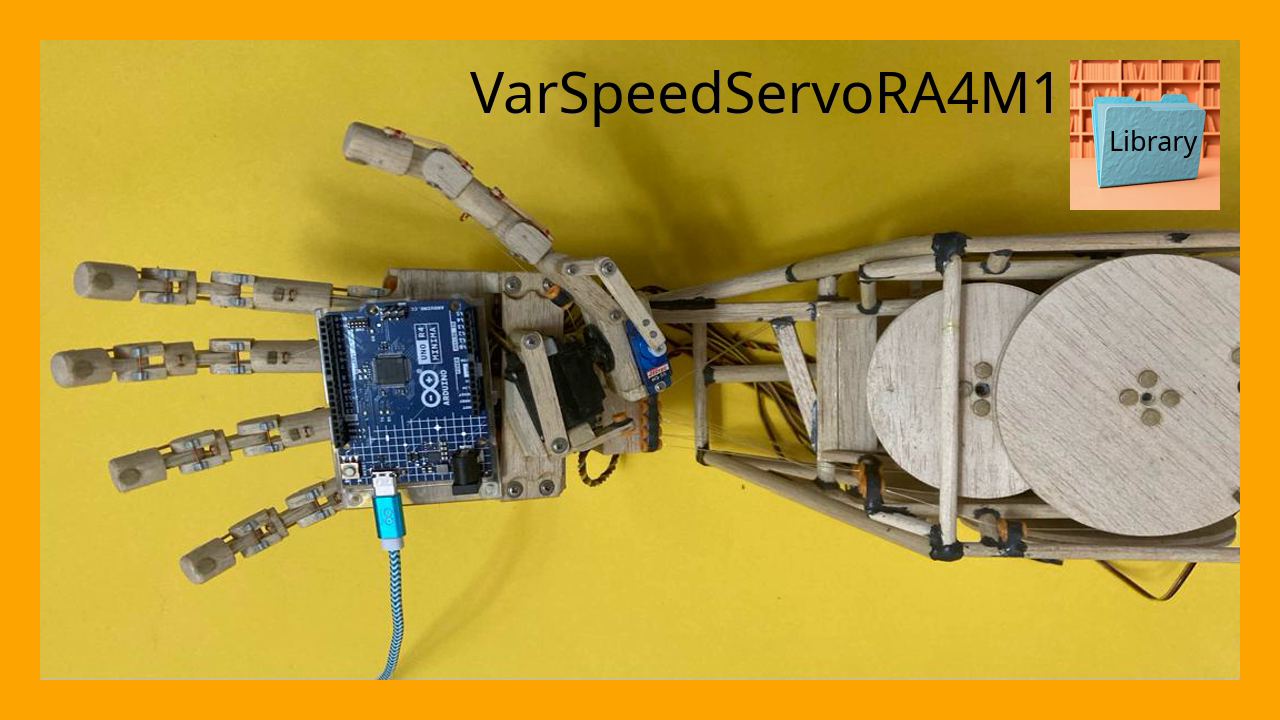
VarSpeedServoRA4M1 is a library for Arduino that enables precise control over servo motors, including speed, position, and movement sequences.
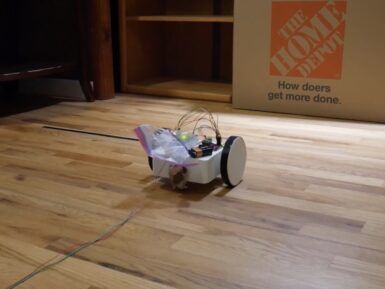
In robotics and several other disciplines, PID (proportional-integral-derivative) control is a way for systems with closed-loop feedback to adjust themselves according to sensor data without overshooting the target. Drones, for example, use PID control to remain stable without wild oscillations caused by over-correction. But implementing PID control can feel overwhelming, so Adam Soileau from element14 Presents built a simple robot for some experimentation. This robot’s only job is to drive forward until it sees a wall, then stop at a specific distance from that wall. That isn’t hard to achieve when a robot is moving at slow pace, because the code can tell the robot to stop moving the moment it reaches the target distance. But when moving fast, the robot has to take braking acceleration into account and that is much harder to predict. PID control is perfect for this situation, because it adjusts motor output in real-time according to the incoming sensor data. In this case, that sensor data comes from an ultrasonic rangefinder mounted to the front of the 3D-printed robot. An Arduino UNO R4 Minima board receives that data and controls the robot’s two motors through H-bridge drivers. That hardware is very straightforward so that Soileau could focus on the PID control. Tuning that is all about balancing the three constant values to get the desired performance. Soileau spent some time working on the Arduino sketch to get the PID control integrated and was eventually able to make the robot act like it should. If you’re interested in using PID control in your next robotics project, then Soileau's video should help you get started.