
CAN-BUS Shield v2
Sold outWith its long travel distance, great communication speed and high reliability, CAN-BUS is one of the most common industrial bus.
Overview
It is commonly found on modern machine tools and as an automotive diagnostic bus.
Thanks to the CAN-BUS, makers are able to hack their cars!
It adopts MCP2515 CAN-BUS controller with SPI interface and MCP2551 CAN transceiver to give you Arduino CAN-BUS capability. Default pinout is OBD-II and CAN standard pinout can be selected by switching jumpers on DB9 interface.
Moreover, it has the TF card slot for data storage and the CS pin that can be set to D4 or D5.
The INT pin can also be set to D2 or D3 by switching jumpers on the back of the shield.
CAN-BUS Shield Works perfectly with Arduino UNO (ATmega328), Arduino Mega (ATmega1280/2560) as well as Arduino Leonardo (ATmega32U4).
Features:
-
Implements CAN V2.0B at up to 1 Mb/s
-
Industrial standard 9 pin sub-D connector
-
OBD-II and CAN standard pinout selectable.
-
Changeable chip select pin
-
Changeable CS pin for TF card slot
-
Changeable INT pin
-
Screw terminal that easily to connect CAN_H and CAN_L
-
Arduino Uno pin headers
-
2 Grove connectors (I2C and UART
-
SPI Interface up to 10 MHz
-
Standard (11 bit) and extended (29 bit) data and remote frames
-
Two receive buffers with prioritized message storage
Conformities
Get Inspired
Easily monitorize your garden's environment with simple components.
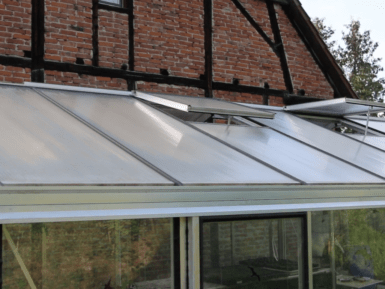
Greenhouses are excellent ways to grow plants due to their compact nature and the fact that they can absorb and store the sun’s light as heat to keep their internal temperature higher than outside. But when it comes to adding ventilation for cooling things down, decreasing the humidity, or simply to avoid rain, most non-commercial ones still rely on someone to manually open or close the windows. This need for automation is what drove Michael Bernhard to create his own greenhouse climate regulation system. This project relies on a Nano Every to read the ambient temperature/humidity as well as control up to six motorized windows via three L298N dual H-bridge drivers. The Nano receives commands and other data over WiFi from an accompanying ESP8266 board for wireless remote control with a mobile phone. Each of these components and their connectors were added to a custom PCB and placed within a simple wooden enclosure to keep moisture out. An LCD at the top shows pertinent information such as the time, temperature, and humidity. The aforementioned WiFi control scheme not only allows for remote control of the windows, but also for the visualization of historical sensors data on a graph. Safety information, including errors and stored EEPROM data, can be viewed on the web application, too. To see more about this project, you can read Bernhard's write-up here on Hackster.io.