
Overview
Tech specs
Power
There is an on-board voltage regulator for higher voltages that protect the Braccio shield. NOTE: The protection doesn’t work for the Arduino Yun if you put the bridge between Vin and 5V on the Arm Robot Shield V1 (greater version of are called Braccio shield and has a power switch on the top of the shield)
Physical Characteristics
- Plastic Parts x 21
- Screws x 63
- Flat Washer x 16
- Hexagon Nut x 7
- Springs x 2
- Servo Motors: 2 x SR 311, 4 x SR 431
- Arduino compatible Shield x 1
- Power Supply 5V, 4A x 1
- Phillips Screwdriver x 1
- Spiral Cable Protection Wrap x 1
Fully assembled Braccio Kit:
Weight |
792 g |
Maximum operating distance range |
80 cm |
Maximum Height |
52 cm |
Base Width |
14 cm |
Gripper Width |
90 mm |
Cable length |
40 cm |
Load Capacity |
Maximum weight at 32 cm operating distance: 150 g |
Maximum weight at the minimal Braccio configuration: 400g |
Servo Technical Specification
SpringRC SR431 - Dual Output Servo |
|
Control Signal |
PWM Analog |
Torque |
@ 4.8V: 169.5 oz-in (12.2 kg-cm) @ 6.0V: 201.4 oz-in (14.5 kg-cm) |
Weight |
2.19 oz (62.0 g) |
Dimentions |
1.65×0.81×1.56 in (42.0×20.5×39.5 mm) |
Speed |
@ 4.8V: 0.20 sec/60° @ 6.0V: 0.18 sec/60° |
Rotation Support |
Dual Bearings |
Gear Material |
Metal |
Rotation Range |
180° |
Connector Type |
J (aka Futaba) |
SpringRC SR311 |
|
Control Signal |
PWM Analog |
Torque |
@ 4.8V: 43.13 oz-in (3.1 kg-cm) @ 6.0V: 52.86 oz-in (3.8 kg-cm) |
Weight |
0.95 oz (27.0 g) |
Dimentions |
1.23×0.65×1.13 in (31.3×16.5×28.6 mm) |
Speed |
@ 4.8V: 0.14 sec/60° @ 6.0V: 0.12 sec/60° |
Rotation Support |
Dual Bearings |
Gear Material |
Metal |
Rotation Range |
180° |
Connector Type |
J (aka Futaba) |
Conformities
Resources for Safety and Products
Manufacturer Information
The production information includes the address and related details of the product manufacturer.
Arduino S.r.l.
Via Andrea Appiani, 25
Monza, MB, IT, 20900
https://www.arduino.cc/
Responsible Person in the EU
An EU-based economic operator who ensures the product's compliance with the required regulations.
Arduino S.r.l.
Via Andrea Appiani, 25
Monza, MB, IT, 20900
Phone: +39 0113157477
Email: support@arduino.cc
Documentation
Assembly video
OSH: Schematics
The TinkerKit braccio is open-source hardware! You can build your own board using the following file:
Get Inspired
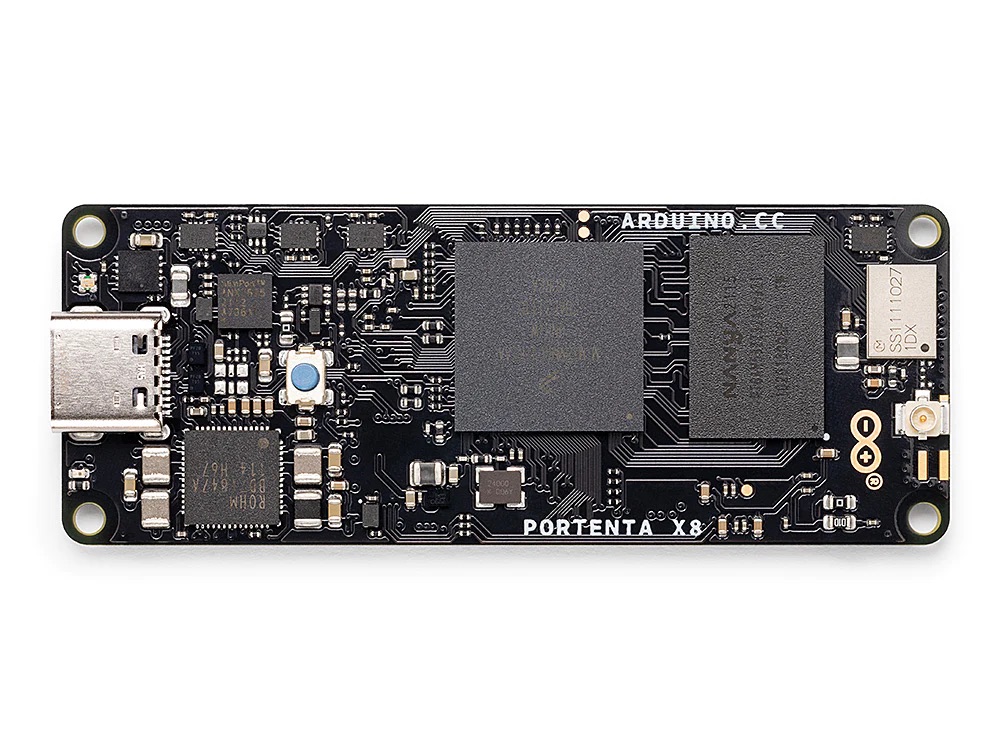
Install FLECS Marketplace on the Portenta X8
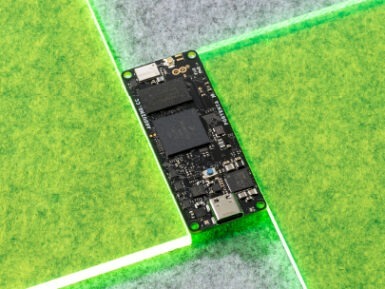
FLECS and Arduino Pro are partnering to make Industry 4.0 easier for you. FLECS is the easy-to-configure and open-source platform that allows industrial users to work with automation solutions dedicated to their machinery just as easily as we all handle the apps on our phone: install, manage and configure via web interface, and let the system keep track of versions and ensure updates. All you need is a Portenta X8 – our powerful, industrial-grade SOM with Linux OS preloaded onboard: connect it to your computer via USB, install FLECS for free (with, literally, one line of code), and access the FLECS UI to pick the right solution for production control, communication, SCADA (Supervisory Control And Data Acquisition), data analysis, fleet management and more. Deploying Linux applications has never been more straightforward: we could say it’s as easy as 1-2-3 – except there are actually only 2 steps to the whole process. “We are excited to offer the huge Arduino user community immediate access to our automation applications, so anyone can build and boost a wide variety of solutions for industrial contexts. It’s all made possible by Portenta X8, a groundbreaking product bringing Linux into the Arduino ecosystem.” – Patric Scholz, Managing Director at FLECS Indeed, while on one side you can now leverage all FLECS solutions in a few commands and clicks, on the other you will be working with one of Arduino Pro’s highest-performance modules: Portenta X8 is basically two industrial products in one, with the power of no less than 9 cores (an NXP i.MX 8M Mini Arm® Cortex®-A53 quad-core, up to 1.8GHz per core + 1x Cortex-M4 up to 400MHz, plus the STMicroelectronics STM32H747 dual-core Cortex-M7 up to 480MHz +M4 32-bit MCU up to 240MHz). And of course, the “superpower” of all Arduino products: being part of a comprehensive ecosystem of open-source hardware, software solutions, Cloud services and amazing community-based support. To find out
FAQs
How many axis does the Braccio robot arm have?
The braccio has a total of 6 axis:
Axis 1 – It is located at the base of a robot, and helps it to rotate from left to right.
Axis 2 – It helps the lower arm of a robot to move in an up and down motion.
Axis 3 – It allows the upper arm of a robot to move forward and backward.
Axis 4 – This axis is known as wrist roll, and it rotates the upper arm of a robot in a circular movement.
Axis 5 – It permits the wrist of the robot’s arm to raise and lower.
Axis 6 – It allows the wrist of the robot’s arm to rotate freely in a circular motion.
All the above six axes are controlled with the help of servo motors.