
Overview
Max Carrier transforms Portenta modules into single-board computers or reference designs that enable edge AI for high-performance industrial, building automation and robotics applications.
Thanks to dedicated high-density connectors, it can be paired with Portenta X8 or H7, allowing you to easily prototype and deploy your industrial projects.
This Arduino Pro carrier further augments Portenta connectivity options with Fieldbus, LoRa®, Cat-M1 and NB-IoT.
Among the many available plug-and-play connectors there are Ethernet, USB-A, audio jacks, microSD, mini-PCIe, FD-CAN and Serial RS232/422/485.
Max Carrier can be powered via external supply (6-36V) or battery via the onboard 18650 Li-ion battery connector with 3.7V battery charger.
Key benefits include:
- Easily prototype industrial applications and minimize time to market
- A powerful carrier exposing Portenta peripherals (e.g. CAN, RS232/422/485, USB, mPCIe)
- Multiple connectivity options (Ethernet, LoRa®, CAT-M1, NB-IoT)
- MicroSD for data logging operations
- Integrated audio jacks (line-in, line-out, mic-in)
- Standalone when battery powered
- Onboard JTAG debugger via micro-USB (with Portenta H7 only)
Prototyping on Portenta projects
The Arduino Portenta Max Carrier is designed to assist developers with their prototypes by exposing the main peripherals of the high-density connectors of the Portenta family boards (H7 and X8). It allows for easy debugging through the JTAG connector and for inspection of the CAN lines through the pins. At the same time, it is the right tool to test Ethernet connectivity as well as to extend connectivity options (CAT-M1, NB-IoT and LoRa®).
Develop your own Industry 4.0 platform
Combine industrial strength and ease of use with Arduino Pro’s Portenta Max Carrier – designed to give you everything you need to implement edge computing in your smart factory or warehouse with simple plug-and-play features. Optimize your manufacturing process and material flows, control machinery remotely and even prevent failures with preventive maintenance: Max Carrier takes your innovation capabilities to the max.
Arduino Iot Cloud
Integrating with Arduino’s IoT Cloud is a simple and fast way to ensure secure communication for all of your connected Things.
TRY THE ARDUINO IOT CLOUD FOR FREE
Need Help?
Check the Arduino Forum for questions about the Arduino Language, or how to make your own Projects with Arduino. If you need any help with your board, please get in touch with the official Arduino User Support as explained in our Contact Us page.
Warranty
You can find your product warranty information here.
*Portenta X8 is not included in the product: Pictures shown are for illustration purposes only.
Tech specs
Connectors |
|
Audio |
|
Memory |
|
Wireless modules |
|
Operating temperatures |
|
Dimensions |
|
Debugging |
|
Power/Battery |
|
Resources for Safety and Products
Manufacturer Information
The production information includes the address and related details of the product manufacturer.
Arduino S.r.l.
Via Andrea Appiani, 25
Monza, MB, IT, 20900
https://www.arduino.cc/
Responsible Person in the EU
An EU-based economic operator who ensures the product's compliance with the required regulations.
Arduino S.r.l.
Via Andrea Appiani, 25
Monza, MB, IT, 20900
Phone: +39 0113157477
Email: support@arduino.cc
Documentation
Learn more
Get Inspired
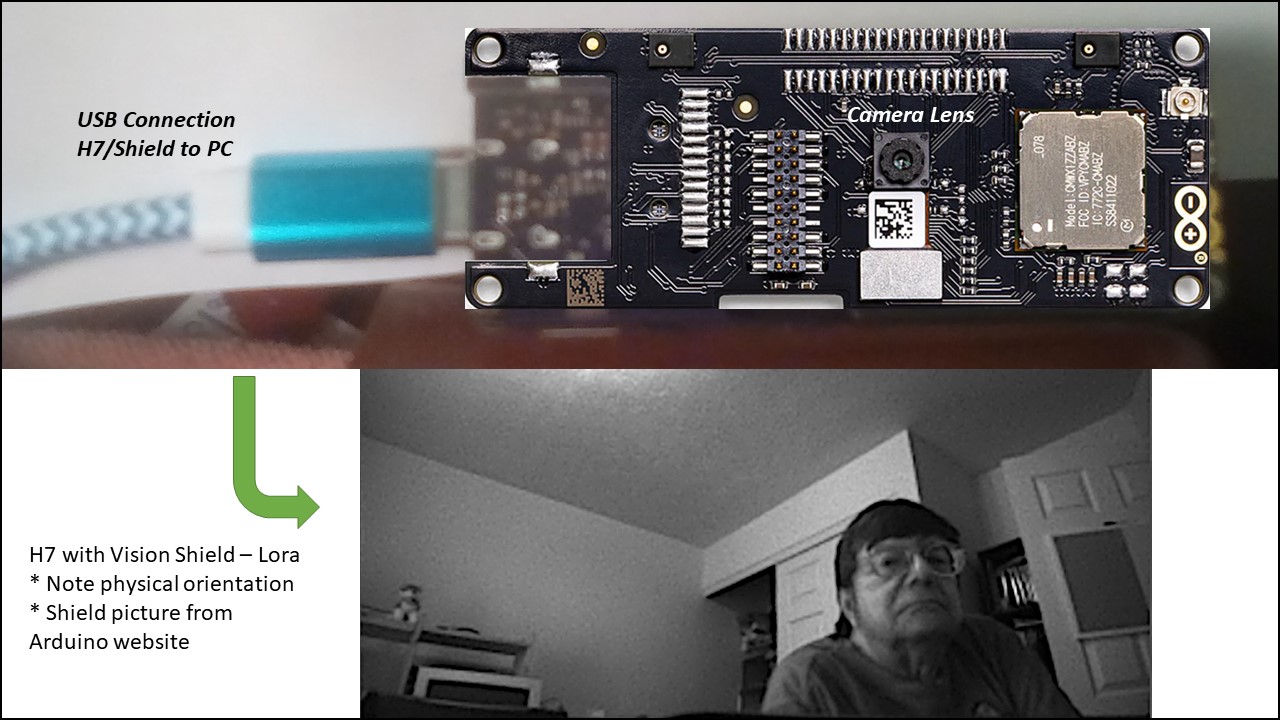
Begins a process of combining Portenta H7 with Vision Shield – LoRa by acquiring, sending, and displaying a camera image via USB/Serial connection.

Jeremy Ellis is a teacher, and as such, wanted a longer-term project that his students could do to learn more about microcontrollers and computer vision/machine learning, and what better way is there than a self-driving car. His idea was to take an off-the-shelf RC car which uses DC motors, add an Arduino Portenta H7 as the MCU, and train a model to recognize target objects that it should follow. After selecting the “RC Pro Shredder” as the platform, Ellis implemented a VNH5019 Motor Driver Carrier, a servo motor to steer, and a Portenta H7 + Vision Shield along with a 1.5” OLED module. After 3D printing a small custom frame to hold the components in the correct orientation, nearly 300 images were collected of double-ringed markers on the floor. These samples were then uploaded to Edge Impulse and labeled with bounding boxes before a FOMO-based object detection model was trained. Rather than creating a sketch from scratch, the Portenta community had already developed one that grabs new images, performs inferencing, and then steers the car’s servo accordingly while optionally displaying the processed image on the OLED screen. With some minor testing and adjustments, Ellis and his class had built a total of four autonomous cars that could drive all on their own by following a series of markers on the ground. For more details on the project, check out Ellis' Edge Impulse tutorial here.