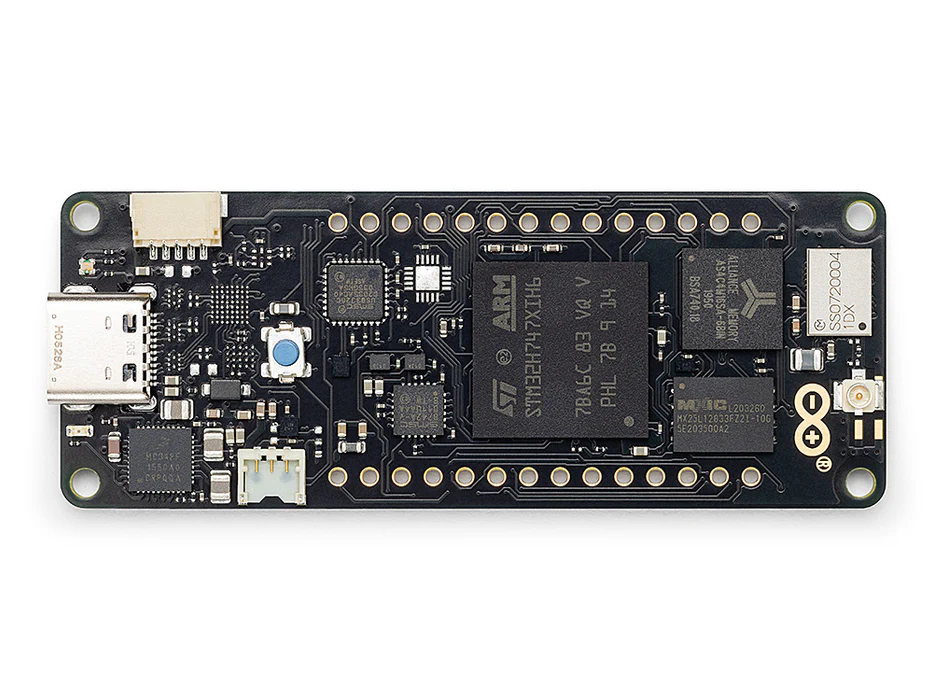
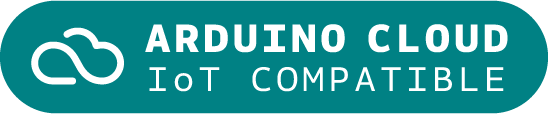
Overview
The Portenta H7 Lite Connected is designed to provide the computational power of the Portenta H7 for AI applications and low-latency control solutions, with a module that is made more cost-effective by removing the high-resolution video interface feature.
It fills the gap between the full H7 and the H7 Lite versions by integrating wireless connectivity, adding yet another option for Arduino Pro clients to build the perfect solution with the right combination of performance and simplicity.
The Portenta H7 Lite Connected simultaneously runs high-level code and real-time tasks thanks to its two processors. For example, it can execute Arduino-compiled and MicroPython code at the same time, and have the two cores communicate via a Remote Procedure Call mechanism that allows calling functions on the other processor seamlessly for real multitasking. Your machine learning algorithms can now run simultaneously alongside low latency sensor/actuator interaction.
Key benefits include:
- Dual Core - Two best-in-class processors in one, running parallel tasks
- AI on the edge - So powerful it can run AI state machines
- Onboard wireless module - Simultaneously manage WiFi and Bluetooth® connectivity
- High-level programming language support (Micropython)
- Security - Onboard secure element for certificates storage and management
The Portenta H7 Lite Connected offers twofold functionality: it can run either like any other embedded microcontroller board, or as the main processor of an embedded computer.
For example, use the Portenta Vision Shield to transform your H7 Lite Connected into an industrial camera capable of performing real-time machine learning algorithms on live video feeds. As the H7 Lite Connected can easily run processes created with TensorFlow™ Lite, you could have one of the cores computing a computer vision algorithm on the fly, while the other carries out low-level operations like controlling a motor or acting as a user interface.
Portenta is the go-to family when performance is key, and the H7 Lite Connected is no exception. We can already envision it as part of a wide range of solutions, including:
- High-end industrial machinery
- Laboratory equipment
- Computer vision
- PLCs
- Robotics controllers
- Mission-critical devices
- High-speed booting computation (ms)
Two Parallel Cores
The Portenta H7 Lite Connected’s main processor is the STM32H747 dual core including a Cortex® M7 running at 480 MHz and a Cortex® M4 running at 240 MHz. The two cores communicate via a Remote Procedure Call mechanism that allows calling functions on the other processor seamlessly. Both processors share all the in-chip peripherals and can run:
- Arduino sketches on top of the Arm® Mbed™ OS
- Native Mbed™ applications
- MicroPython / JavaScript via an interpreter
- TensorFlow™ Lite
A New Standard for Pinouts
The Portenta family adds two 80-pin high-density connectors at the bottom of the module. This ensures scalability for a wide range of applications: simply upgrade your Portenta to the one suiting your needs.
USB-C® Multipurpose Connector
The module’s programming connector is a USB-C port that can also be used for power, as a USB Hub, or to deliver power to OTG connected devices.
Arduino IoT Cloud Compatible
Use your MKR board on Arduino's IoT Cloud, a simple and fast way to ensure secure communication for all of your connected Things.
TRY THE ARDUINO IOT CLOUD FOR FREE
Need Help?
Check the Arduino Forum for questions about the Arduino Language, or how to make your own Projects with Arduino. If you need any help, please get in touch with the official Arduino User Support as explained in our Contact Us page.
Warranty
You can find your warranty information here.
Tech specs
Microcontroller |
STM32H747XI dual Cortex®-M7+M4 32bit low power Arm® MCU (datasheet) |
CONNECTIVITY |
Ethernet, WiFi, Bluetooth® Low Energy |
Secure Element (default) |
Microchip ATECC608 |
Power Supply (USB/VIN) |
5V |
Supported Battery |
Li-Po Single Cell, 3.7V, 700mAh Minimum (integrated charger) |
Circuit Operating Voltage |
3.3V |
Current Consumption |
2.95 μA in Standby mode (Backup SRAM OFF, RTC/LSE ON) |
Timers |
22x timers and watchdogs |
UART |
4x ports (2 with flow control) |
Ethernet PHY |
10 / 100 Mbps (through expansion port only) |
SD Card |
Interface for SD Card connector (through expansion port only) |
Operational Temperature |
-40 °C to +85 °C |
MKR Headers |
Use any of the existing industrial MKR shields on it |
High-density Connectors |
Two 80 pin connectors will expose all of the module's peripherals to other devices |
Camera Interface |
8-bit, up to 80 MHz |
ADC |
3× ADCs with 16-bit max. resolution (up to 36 channels, up to 3.6 MSPS) |
DAC |
2× 12-bit DAC (1 MHz) available, only one is accessible by the user through the external A6 pin |
USB-C |
Host / Device, High / Full Speed, Power delivery |
Conformities
Resources for Safety and Products
Manufacturer Information
The production information includes the address and related details of the product manufacturer.
Arduino S.r.l.
Via Andrea Appiani, 25
Monza, MB, IT, 20900
https://www.arduino.cc/
Responsible Person in the EU
An EU-based economic operator who ensures the product's compliance with the required regulations.
Arduino S.r.l.
Via Andrea Appiani, 25
Monza, MB, IT, 20900
Phone: +39 0113157477
Email: support@arduino.cc
Documentation
Learn more
Get Inspired
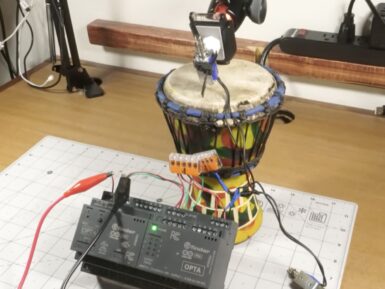
Makers have long asked the question “why bother with an expensive PLC when I can just use an Arduino?” The answer comes down to the priorities and needs of industrial clients. In a factory automation setting, the client will prioritize durability, reliability, and serviceability over the one-time purchase price of the device itself. But to prove that Arduino’s professional turnkey solutions are just as easy to use as their developer-focused educational counterparts, Jeremy Cook leveraged an Arduino Opta micro PLC to build a drum machine. This isn’t any old drum machine that plays sound samples or synthesized notes, but rather a robotic drum machine that makes noise by banging on stuff like a true percussion instrument. Cook could have built this with any Arduino board and a few relays, but instead chose to implement the Opta and new Opta Digital Expansion. That is robust enough for serious commercial and industrial applications, but is still simple to program with the familiar Arduino IDE. Programmers can also use conventional PLC languages if they prefer. In this case, Cook made noise with relays and solenoids. The Opta has four built-in relays and Cook’s sketch flips one of them to make a sound analogous to a hi-hat. Cook added an Arduino Pro Opta Ext D1608S module with its solid-state relays for the other two “drums.” One of those fires a solenoid that taps a small hand drum (the kick drum sound), while the other controls a solenoid that hits a power supply enclosure (the snare sound). Together, those three sounds can cover the basics of a drum track. Cook’s sketch is a drum sequencer program that stores each sound sequence as array, looping through them until turned off. An Opta may be overkill for a project like this one, but this does a great job of demonstrating the ease at which an Arduino user can transition to professional PLC work.