
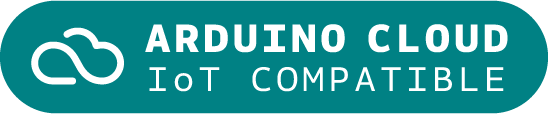
Machine Vision Bundle
A rapid solution for embedded machine learning (ML) combining vision, audio and connectivity. Open the lenses to a new territory of lean and efficient image processing applications for your Arduino projects.
Overview
The Arduino Portenta Vision Shield is a production-ready expansion for the powerful Arduino Portenta H7. It adds a low-power camera, two microphones, and connectivity; everything you need for the rapid development of edge ML applications.
The Portenta H7 simultaneously runs high-level code along with real-time tasks. The
H7's main processor is a dual-core STM32H747 including a Cortex® M7 running at 480MHz and a Cortex® M4 running at 240MHz. The two cores communicate via a Remote Procedure Call mechanism that allows seamless calling of functions on the other processor.
Both processors share all the in-chip peripherals and can run:
- Arduino sketches on top of the Arm® Mbed™ OS
- Native Mbed™ applications
MicroPython / JavaScript (via an interpreter)
TensorFlow™ Lite
Moreover, the onboard wireless module allows the simultaneous management of WiFi and Bluetooth® connectivity on the Portenta H7.
The Portenta Vision Shield brings industry-rated vision and audio capabilities to your Portenta H7. This hardware add-on lets you run embedded computer vision applications, connect wirelessly or via Ethernet to the Arduino Cloud or your own infrastructure, and activate your system using sound detection.
The Vision shield comes with a 324x324 pixels camera module that contains an ultra low power image sensor designed for always-on vision devices and applications. The high sensitivity image sensors can capture gestures, ambient light, proximity sensing and object identification.
There’s a plethora of applications you can deploy with Portenta H7 and Portenta Vision Shield. The demonstration below shows how to implement an accurate digits recognition system using Edge Impulse. Digits recognition using computer vision is desirable in many application and market areas, such as grocery retail, manufacturing, utility metering, and administration.
Learn how to implement accurate digit recognition using Edge Impulse.
Check out the documentation to easily implement Portenta H7 and Portenta Vision Shield in your projects.
Arduino IoT Cloud Compatible
Use your MKR board on Arduino's IoT Cloud, a simple and fast way to ensure secure communication for all of your connected Things.
Need Help?
Check the Arduino Forum for questions about the Arduino Language, or how to make your own projects with Arduino. If you need any help with your board, please get in touch with the official Arduino User Support as explained on our Contact Us page.
Warranty
You can find your board warranty information here.
Tech specs
The Machine Vision Bundle includes:
Resources for Safety and Products
Manufacturer Information
The production information includes the address and related details of the product manufacturer.
Arduino S.r.l.
Via Andrea Appiani, 25
Monza, MB, IT, 20900
https://www.arduino.cc/
Responsible Person in the EU
An EU-based economic operator who ensures the product's compliance with the required regulations.
Arduino S.r.l.
Via Andrea Appiani, 25
Monza, MB, IT, 20900
Phone: +39 0113157477
Email: support@arduino.cc
Get Inspired
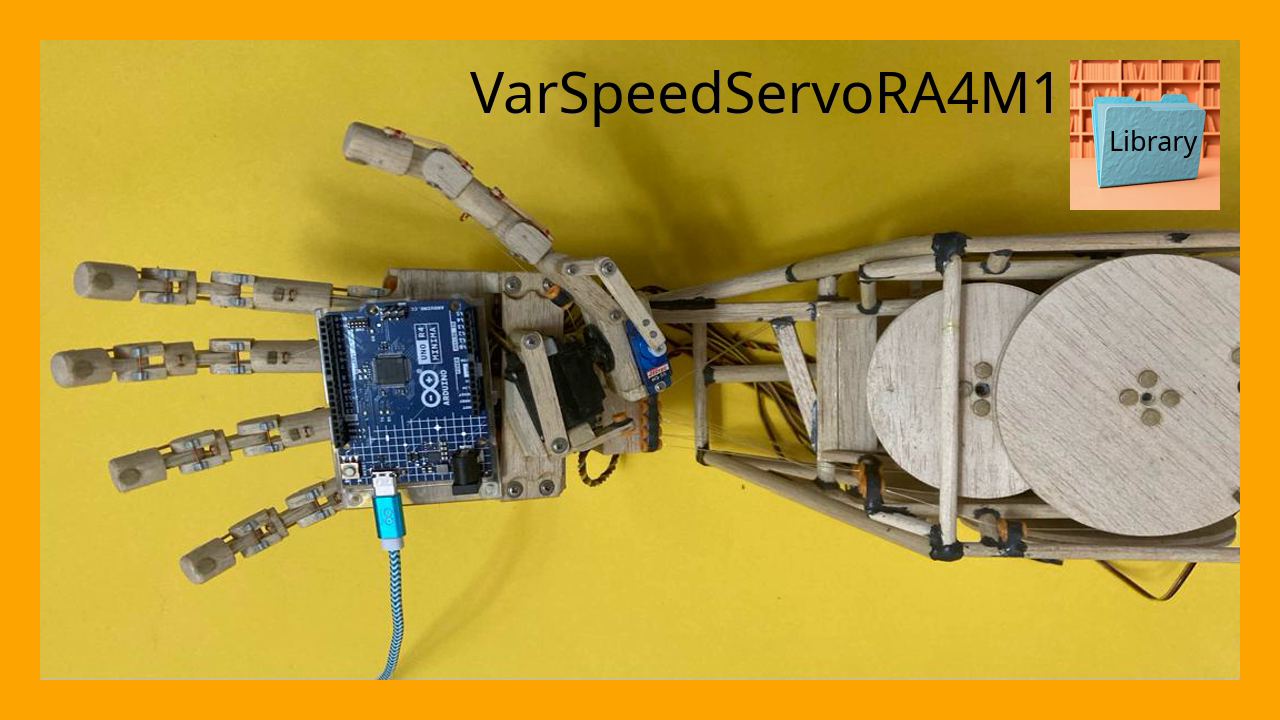
VarSpeedServoRA4M1 is a library for Arduino that enables precise control over servo motors, including speed, position, and movement sequences.
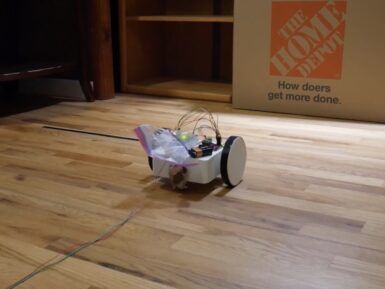
In robotics and several other disciplines, PID (proportional-integral-derivative) control is a way for systems with closed-loop feedback to adjust themselves according to sensor data without overshooting the target. Drones, for example, use PID control to remain stable without wild oscillations caused by over-correction. But implementing PID control can feel overwhelming, so Adam Soileau from element14 Presents built a simple robot for some experimentation. This robot’s only job is to drive forward until it sees a wall, then stop at a specific distance from that wall. That isn’t hard to achieve when a robot is moving at slow pace, because the code can tell the robot to stop moving the moment it reaches the target distance. But when moving fast, the robot has to take braking acceleration into account and that is much harder to predict. PID control is perfect for this situation, because it adjusts motor output in real-time according to the incoming sensor data. In this case, that sensor data comes from an ultrasonic rangefinder mounted to the front of the 3D-printed robot. An Arduino UNO R4 Minima board receives that data and controls the robot’s two motors through H-bridge drivers. That hardware is very straightforward so that Soileau could focus on the PID control. Tuning that is all about balancing the three constant values to get the desired performance. Soileau spent some time working on the Arduino sketch to get the PID control integrated and was eventually able to make the robot act like it should. If you’re interested in using PID control in your next robotics project, then Soileau's video should help you get started.