
J-Link PLUS Compact
Sold outUSB powered JTAG debug probe supporting a large number of CPU cores.
Based on a 32-bit RISC CPU, it can communicate at high speed with the supported target CPUs.
SEGGER J-Link PLUS Compact is used around the world in tens of thousand places for development and production (flash programming) purposes.
Overview
Get the SEGGER J-Link PLUS Compact debug probe: a compact version of the J-Link PLUS. Mounts securely & unobtrusively into development and end user equipment.
Based on 32-bit RISC CPU, it communicates at high speed with supported target CPUs.
Thanks to a small size with two mounting holes, it can be placed into existing equipment housings.
Space can also be reserved for direct-to-PCB mounting.
All major IDEs (Eclipse & GDB-based IDEs) support J-Link debug probes, as does SEGGER Embedded Studio. 500,000 J-Links have been shipped so far, making this probably the most popular debug probe on the market for Arm cores and the de-facto standard.
Further Advantages
The SEGGER J-Link PLUS Compact has a built-in VCOM functionality and integrated licenses for unlimited breakpoints in flash memory, RDI/RDDI and J-Flash. It supports direct download into RAM and flash memory. It has a broad range of supported microcontrollers and CPUs.
Box Contents
- SEGGER J-Link PLUS Compact debug probe
- Micro USB cable
- 1" 20-pin ribbon cable (18 cm)
- Includes free software updates and one year of email support.
SEGGER J-Link debuggers are the most popular choice for optimizing the debugging and flash programming experience.
Documentation
Debugging with the Arduino IDE 2.0
Learn how to set up a Zero board, J-Link and Atmel-ICE debuggers with the Arduino IDE 2.0, and how to debug a program.
Using the Segger J-Link debugger with the MKR boards
Learn how to set up a MKR board with the Segger J-link debugger.
Get Inspired
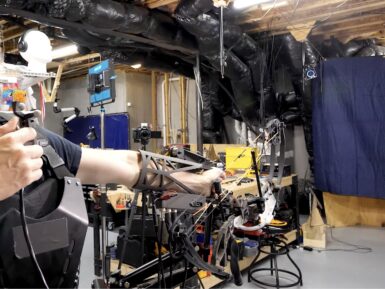
After becoming frustrated at his lack of archery skills and not wanting to spend an eternity practicing getting better, Shane Wighton (known as Stuff Made Here on YouTube) sought to build a rig that could automatically correct his aim for the perfect shot every time. The device is comprised of a rigid sleeve that fits over the wearer’s forearm, along with a pair of stepper motors that can adjust where the bow is pointing either vertically or horizontally via a rack-and-pinion. These motors are driven by an Adafruit microcontroller running CircuitPython and a couple of motor driver modules that provide the necessary current. But that's not all, he also created a small rig that uses an Arduino Uno and servo motor to autonomously fling targets into the air. Target tracking is achieved by having a set of eight OptiTrack cameras around the room monitor the space for tiny gray spheres, and through the use of a special triangulation algorithm, they can accurately determine where both the arrow is pointing and where the target is in 3D space. Initially, the system missed all of its shots due to poor software and the wrong kind of bow, so Wighton completely rewrote his program and switched to a compound bow instead. Once everything had been corrected, the software was able to predict where a flying target would end up according to its speed, and thus had the ability to intercept it. The Auto-Aiming Bow could also hit a target the size of a 3mm-wide circle with scary precision.