
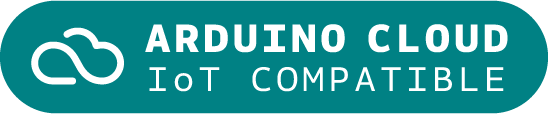
Arduino Opta WiFi
Discover everything our most versatile Opta micro PLC has to offer: designed for engineers who need to keep their options open.
Overview
Arduino Opta is a secure, easy-to-use micro PLC with Industrial IoT capabilities.
Designed in partnership with Finder – leading industrial and building automation device manufacturer – Opta allows professionals to scale up automation projects while leveraging the Arduino ecosystem. Supporting both Arduino sketch and standard PLC languages, including LD (Ladder Logic Diagram) and FBD (Function Block Diagram), it was designed with PLC engineers in mind.
Its powerful STM32H747XI dual-core Cortex®-M7 +M4 MCU allows users to perform real-time control, monitoring and implement predictive maintenance applications.
Secure and durable by design, it supports OTA firmware updates and ensures data security from the hardware to the Cloud thanks to the onboard secure element and X.509 Standard compliance. In addition, Opta undergoes regular assessments to uphold and improve its cybersecurity posture.
All while maintaining Arduino Pro’s signature easy deployment in production thanks to a vast range of readily available software libraries and Arduino sketches.
Last but not least, various connectivity options make keeping everything under control effortless via real-time dashboards combined with the intuitive Arduino Cloud (or third-party services).
Opta comes in three variants so you can choose the best option for your project. Opta WiFi features Ethernet onboard and USB-C programming ports, RS485 half duplex connectivity interface, and Wi-Fi/Bluetooth® Low Energy connectivity.
More than you need? Check out Opta RS485 or Opta Lite.
Program it with the Arduino PLC IDE!
The Arduino PLC IDE makes PLC programming easy. Choose any of the 5 programming languages defined by the IEC 61131-3 standard (Ladder, Functional Block Diagram, Structured Text, Sequential Function Chart or Instruction List) and quickly code PLC applications or port existing ones to Arduino Opta.
Key benefits include:
- Easy and fast software development, starting from ready-to-use Arduino sketches, tutorials and libraries
- Support for standard IEC 61131-3 PLC languages
- Fieldbus integration via Modbus TCP (ethernet) and Modbus RTU (serial RS485)
- Seamless IoT connectivity (Ethernet/Wi-Fi/Bluetooth® Low Energy)
- Real-time remote monitoring via intuitive Arduino Cloud dashboards (or third-party services)
- Security at the hardware level thanks to onboard secure element and X.509 Standard compliance
- Secure OTA firmware updates and Cloud device management
- High-power relay switching (4 x 2.3 kW)
- Reliable by design, thanks to industrial certifications and Finder’s expertise in switching technology
- Easy to install, with DIN rail compatibility
Opt in to industrial automation
Integrate a solid and reliable micro PLC with your existing machines, devices and production lines – also in combination with other elements in the modular and versatile Arduino ecosystem, from small and smart sensor-packed modules to SOMs to gateways, for end-to-end solutions that can be customized to meet any need.
Quality by design
Arduino Pro partnered with Finder, a leader in the field of electromechanical and electronic components with 65+ years of excellence and expertise to its name, to create a product with high-quality production specs for even the most demanding work conditions in industrial environments.
Need Help?
Check the Arduino Forum for questions about the Arduino Language, or how to make your own Projects with Arduino. If you need any help with your product, please get in touch with the official Arduino User Support as explained in our Contact Us page.
Warranty
You can find your product warranty information here.
Tech specs
Input | 8x configurable digital / analog (0-10V) input |
Processor | STM32H747XI Dual ARM® Cortex®:
|
Connectivity | Support 10/100 Ethernet (TCP/IP or Modbus TCP) USB-C Wi-Fi + Bluetooth® Low Energy RS485 half duplex |
Memory | 1MB RAM (programming) 2MB internal + 16MB Flash QSPI |
RTC | Typical 10 days power retention at 25°C NTP sync available through ethernet |
IP protection | IP20 |
Output | 4x relays (250 V AC - 10 A) |
Programming languages |
|
Security | ATECC608B Secure element |
Supply voltage | 12…24 V DC |
Operating Temperature | -20 °C to +50 °C (-4°F to 122°F) |
Certifications | cULus listed, ENEC, CE |
Resources for Safety and Products
Manufacturer Information
The production information includes the address and related details of the product manufacturer.
Arduino S.r.l.
Via Andrea Appiani, 25
Monza, MB, IT, 20900
https://www.arduino.cc/
Responsible Person in the EU
An EU-based economic operator who ensures the product's compliance with the required regulations.
Arduino S.r.l.
Via Andrea Appiani, 25
Monza, MB, IT, 20900
Phone: +39 0113157477
Email: support@arduino.cc
Documentation
Learn more
Get Inspired
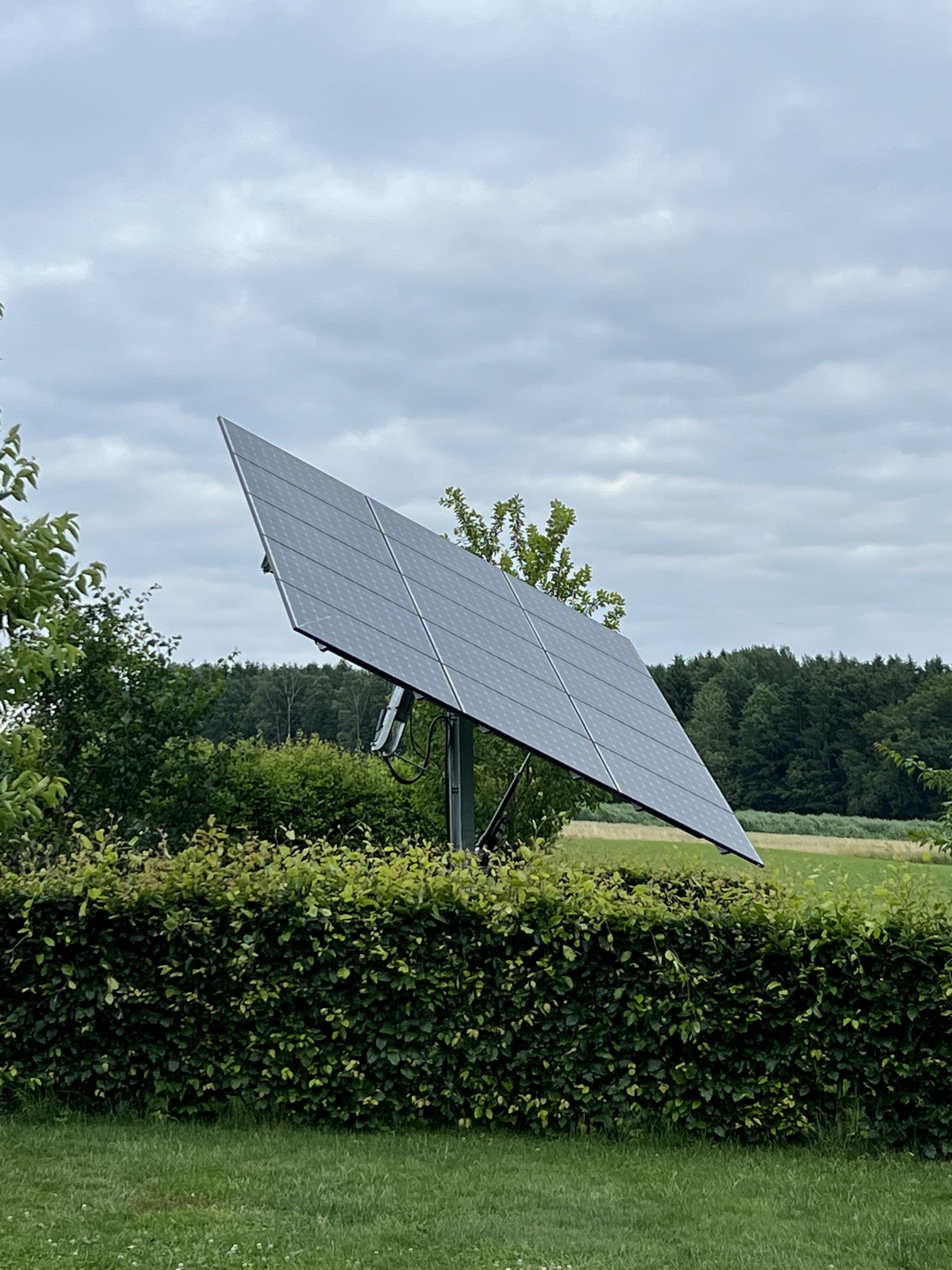
A fully-operational and field-tested photovoltaic plant that automatically sets the optimal angles based on time and location.
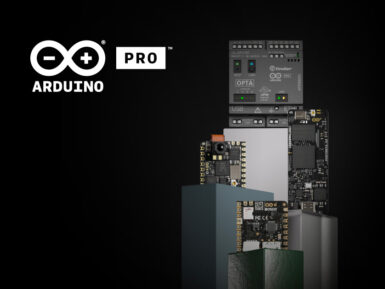
Mark your calendars: May 23rd-25th we’ll be at SPS Italia, one of the country’s leading fairs for smart, digital, sustainable industry and a great place to find out what’s new in automation worldwide. We expect a lot of buzz around AI for IoT applications – and, of course, we’ll come prepared to give our own, open-source perspective on the AIoT trend. At Arduino Pro’s booth C012, pavilion 7, our experts will be presenting some of the latest additions to our ever-growing ecosystem, which includes everything companies need to fully embrace digital transformation with professional performance paired with Arduino’s ease of use and open-source philosophy. You can explore our complete digital brochure here, but let us point out some recent highlights. Meet the Arduino Pro ecosystem at SPS Italia 2023 Over the years, Arduino Pro has built quite the presence on the market with SOMs like the Portenta H7 and X8, recently joined by the Portenta C33: a cost-effective, high-performance option that makes automation accessible to more users than ever, based on the RA6M5, an Arm® Cortex®-M33 microcontroller from Renesas.Our Nicla family of ultra-compact boards also expanded: after Nicla Sense ME and Nicla Vision, Nicla Voice packs all the sensors, intelligence and connectivity you need for speech recognition on the edge, leveraging AI and ML. What’s more, the Arduino ecosystem also includes turnkey solutions like the Portenta Machine Control and the new Opta, our very first microPLC, designed in partnership with Finder to support the Arduino programming experience with the main PLC standard languages – and available in 3 variants with different connectivity features: Opta Lite, Opta RS485, and Opta WiFi. Both the Portenta Machine Control and Opta can be programmed via the new PLC IDE, designed to help you boost production and build automation with your own Industry 4.0 control system. Finally, since SPS Italy’s last edition we have