
CAN-BUS Shield v2
Sold outWith its long travel distance, great communication speed and high reliability, CAN-BUS is one of the most common industrial bus.
Overview
It is commonly found on modern machine tools and as an automotive diagnostic bus.
Thanks to the CAN-BUS, makers are able to hack their cars!
It adopts MCP2515 CAN-BUS controller with SPI interface and MCP2551 CAN transceiver to give you Arduino CAN-BUS capability. Default pinout is OBD-II and CAN standard pinout can be selected by switching jumpers on DB9 interface.
Moreover, it has the TF card slot for data storage and the CS pin that can be set to D4 or D5.
The INT pin can also be set to D2 or D3 by switching jumpers on the back of the shield.
CAN-BUS Shield Works perfectly with Arduino UNO (ATmega328), Arduino Mega (ATmega1280/2560) as well as Arduino Leonardo (ATmega32U4).
Features:
-
Implements CAN V2.0B at up to 1 Mb/s
-
Industrial standard 9 pin sub-D connector
-
OBD-II and CAN standard pinout selectable.
-
Changeable chip select pin
-
Changeable CS pin for TF card slot
-
Changeable INT pin
-
Screw terminal that easily to connect CAN_H and CAN_L
-
Arduino Uno pin headers
-
2 Grove connectors (I2C and UART
-
SPI Interface up to 10 MHz
-
Standard (11 bit) and extended (29 bit) data and remote frames
-
Two receive buffers with prioritized message storage
Conformities
Get Inspired
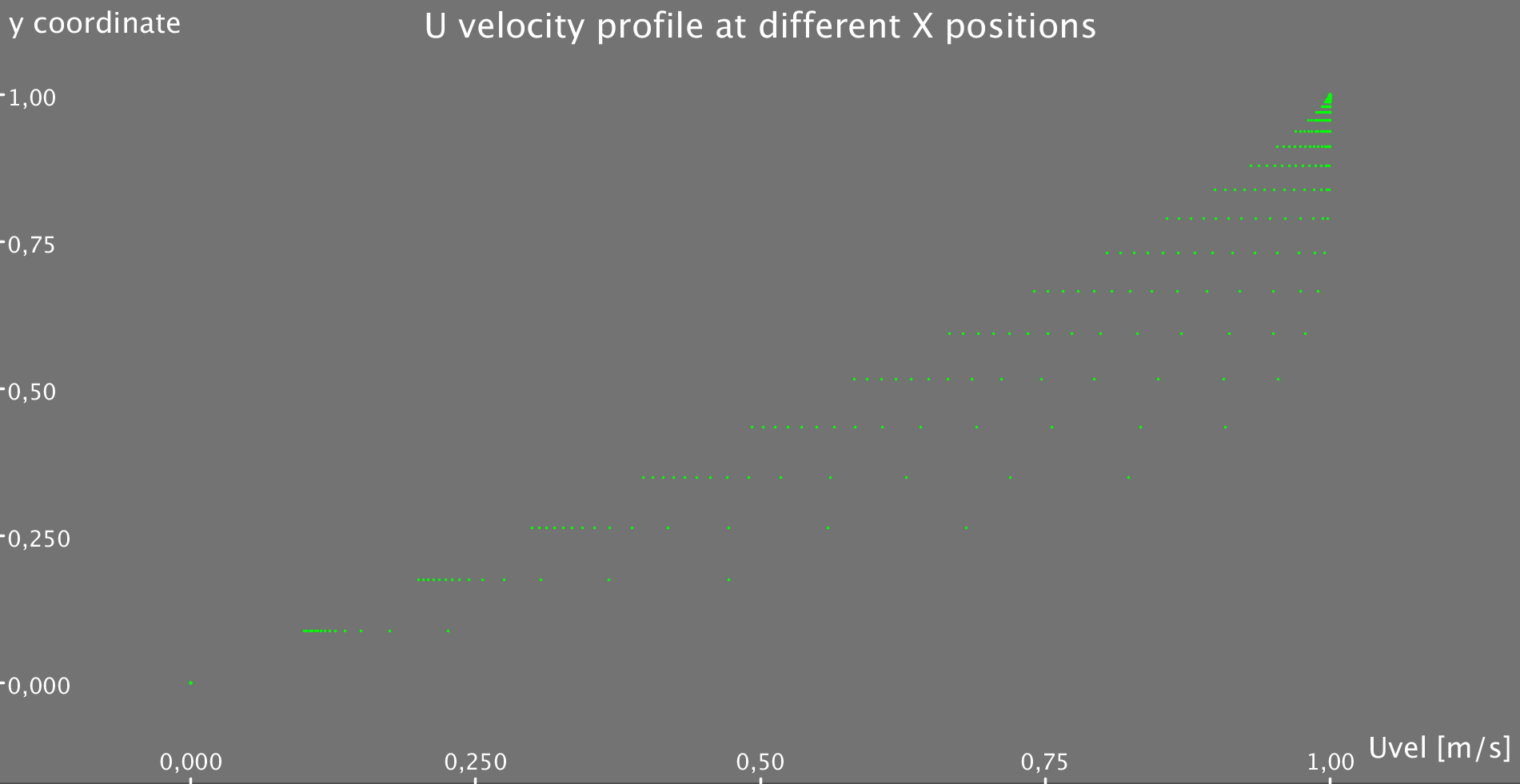
Simple Code that allows you to solve the 2D flow equation for a flat plate Boundary Layer!!
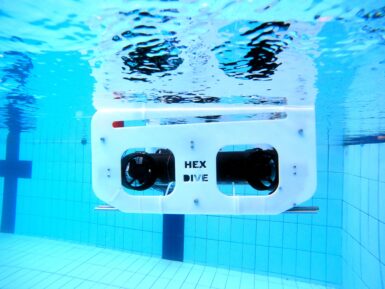
Who doesn’t want to explore underwater? To take a journey beneath the surface of a lake or even the ocean? But a remotely operated vehicle (ROV), which is the kind of robot you’d use for such an adventure, isn’t exactly the kind of thing you’ll find on the shelf at your local Walmart. You can, however, follow this guide from Ranuga Amarasinghe to build your own ROV for some aquatic fun. Amarasinghe is a 16-year-old Sri Lankan student and this is actually the second iteration of his ROV design. As such, he's dubbed it “ROV2” and it appears to be quite capable. All of its electronics sit safely within a 450mm length of sealed PVC tube. That mounts onto the aluminum extrusion frame structure that also hosts the six thrusters powered by drone-style brushless DC motors. ROV2’s brain is an Arduino Mega 2560 board and it drives the BLDC motors through six electronic speed controllers (ESCs). It receives control commands from the surface via an umbilical. The operator holds a Flysky transmitter that sends radio signals to a receiver floating on the water. An Arduino UNO Rev3 reads those and then communicates the motor commands to the Mega through the tethered serial connection. That limits the maximum length of the tether to about 40 meters, which subsequently limits the maximum operating depth. With the specified lithium battery pack, ROV2 can traverse the depths for 30-45 minutes. And when equipped with the 720p FPV camera, pilots can see and record all of the underwater action.