
ROCK 4 Model C + 4G
ROCK 4C+ SBC based on the powerful Rockchip RK3399‑T SoC
Hexa-core processor with Arm® big.LITTLE™ dual Arm Cortex® A72, quad Cortex-A53 CPU, and Arm Mali™ T860MP4 GPU
4GB 64-bit RAM and eMMC socket
Power on/off button, integrated fan control, external antenna & audio jack
Dual micro-HDMI ports supporting displays of up to 4Kp60 resolution
Bluetooth 5.0 with BLE, Gigabit Ethernet and Wireless LAN
Overview
The ROCK 4C+ is a reliable, multifunctional and high-performing single-board computer based on a robust Rockchip RK3399T SoC, Dual Cortex® A72 CPU and Arm Mali™ T860MP4 GPU. Developed by OKdo Technology in collaboration with Radxa, the board incorporates class-leading functionality suitable for multiple multimedia and industrial applications, ensuring outstanding reliability.
With the onboard On/Off power button, ROCK 4C+ is an energy-efficient single-board computer. It also features multiple storage capabilities, such as 4GB 64-bit RAM and eMMC socket, an integrated fan control, an external antenna, an audio jack, dual-display support and two micro-HDMI ports supporting displays up to 4Kp60 resolution.
ROCK 4C+ is extremely practical, as it is compatible with multiple software options, including Android, Debian/Ubuntu Linux, the full implementation of the Arm architecture v8A instructions set, and others. The 40P GPIO extension supports a wide range of interface options, providing the board with high connectivity capabilities, such as Bluetooth 5.0 with BLE, Gigabit Ethernet and Wireless LAN and extensive compatibility with a wide range of accessories.
What are the main benefits of the ROCK 4C+?
- On board on/off power button
- Integrated fan control forthermal management
- Dual-display support
- Two micro-HDMI ports supporting displays up to 4Kp60 resolution
- Multiple connectivity capabilities so less add on hardware required, including Bluetooth 5.0 with BLE, Gigabit Ethernet & Wireless LAN
- A 40P GPIO expansion header provides extensive compatibility with a wide range of accessories
- Get more multiple memory options, including 4GB RAM and a speed eMMC socket
Key technical features of the ROCK 4C+:
- Rockchip RK3399T SoC
- Arm® big.LITTLE™ technology (Dual Cortex®-A72 frequency 1.5GHz and a Quad Cortex-A53 frequency 1.0GHz)
- Arm Mali™ T860MP4 GPU, supporting OpenGL® ES 1.1 /2.0 /3.0 /3.1 /3.2, Vulkan® 1.0, Open CL® 1.1 1.2, DirectX® 11.1
- Dual Arm Cortex – M0
- Dual channel 4GB 64bit LPDDR4
- eMMC connectors
- Display supporting mirror and extended modes
- Dual micro-HDMI
- MIPI DSI
- H.265/VP9 (HEVC) hardware decode (up to 4Kp60)
- H.264 hardware decode (up to 1080p60)
- USB TypeC™ power input
Interfaces:
- 802.11 b/g/n/ac (WiFi 5) Wireless LAN
- Bluetooth 5.0 with BLE
- 1 x micro-SD card slot
- 2 x HDMI ports supporting displays up to 4Kp60 resolution and 2Kp60
- 2 x USB2 HOST ports
- 1 x USB3 OTG/HOST port, 1x USB3 HOST port
- 1 x Gigabit Ethernet port (supports PoE with addon PoE HAT)
- 1 x camera port (2lane MIPI CSI)
- 1 x display port (4lane MIPI DSI)
- 40 x user GPIO supporting a wide range of interface options: 2 x UART, 2 x SPI bus, 2 x I2C bus, 1 x PCM/I2S, 1 x SPDIF, 1 x PWM, 1 x ADC, 6 x GPIO, 2 x 5V DC power in, 2 x 3.3V power pin.
Supported software:
Full implementation of the Arm architecture v8A instructions set, Arm NEON Advanced SIMD (single instructions, multiple data) support for accelerating media and signal processing
Armv8 cryptography extensions
TrustZone® technology support
Debian/Ubuntu Linux support
Android 7.1/Android 5.0/Android 10/Android 11 support
GPU enabled Al stack
Hardware access/control library for Linux/Android
*Please note this is the bulk variant containing 100 units of the ROCK 4C+ model
Documentation
Get Inspired
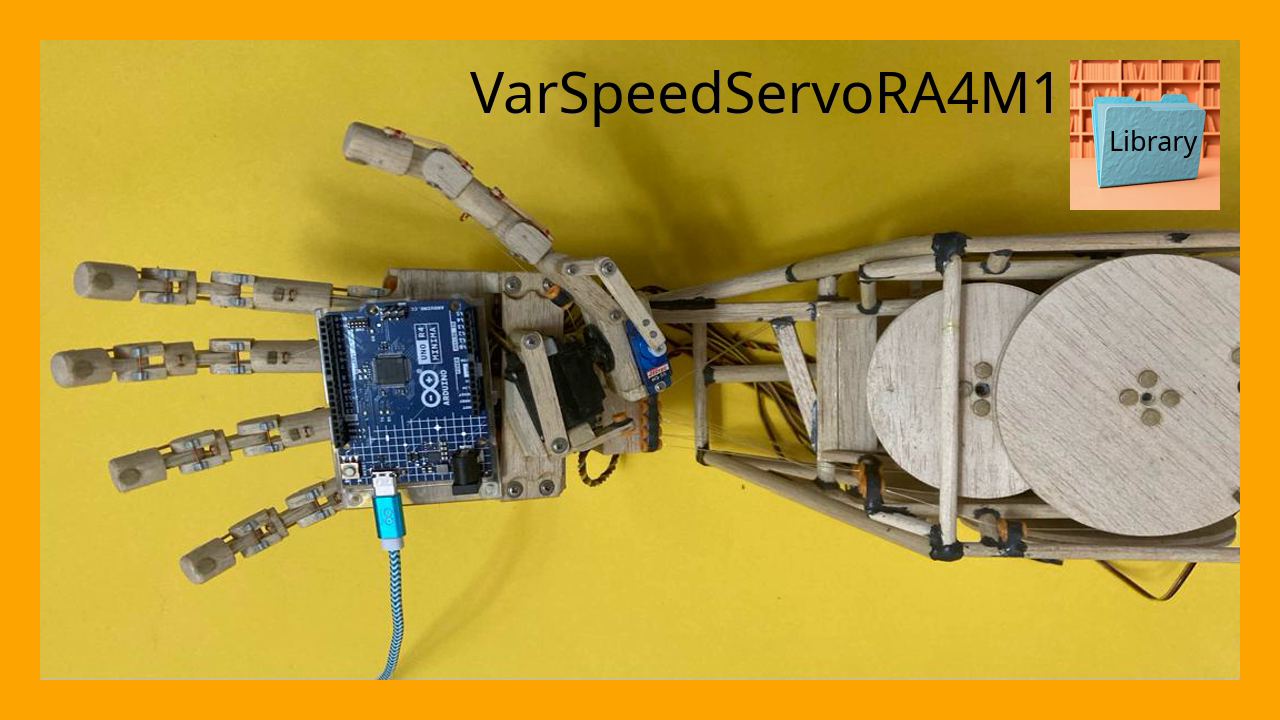
VarSpeedServoRA4M1 is a library for Arduino that enables precise control over servo motors, including speed, position, and movement sequences.
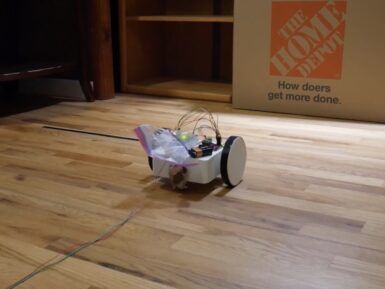
In robotics and several other disciplines, PID (proportional-integral-derivative) control is a way for systems with closed-loop feedback to adjust themselves according to sensor data without overshooting the target. Drones, for example, use PID control to remain stable without wild oscillations caused by over-correction. But implementing PID control can feel overwhelming, so Adam Soileau from element14 Presents built a simple robot for some experimentation. This robot’s only job is to drive forward until it sees a wall, then stop at a specific distance from that wall. That isn’t hard to achieve when a robot is moving at slow pace, because the code can tell the robot to stop moving the moment it reaches the target distance. But when moving fast, the robot has to take braking acceleration into account and that is much harder to predict. PID control is perfect for this situation, because it adjusts motor output in real-time according to the incoming sensor data. In this case, that sensor data comes from an ultrasonic rangefinder mounted to the front of the 3D-printed robot. An Arduino UNO R4 Minima board receives that data and controls the robot’s two motors through H-bridge drivers. That hardware is very straightforward so that Soileau could focus on the PID control. Tuning that is all about balancing the three constant values to get the desired performance. Soileau spent some time working on the Arduino sketch to get the PID control integrated and was eventually able to make the robot act like it should. If you’re interested in using PID control in your next robotics project, then Soileau's video should help you get started.