
Grove - Speech Recognizer
The Grove speech recognizer is a module designed for application in the smart home, toy, robot or anything you would like to control with voice commands.
Overview
The board includes a Nuvoton ISD9160, a microphone, 1 SPI flash, 1 grove connector, 1 speaker connector and 1 led to show to your voice activity.
Nuvoton ISD9160 is (SoC) Chipcorder that based on Cortex™-M0, it provides performance and the energy efficiency needed for voice control applications. The microphone on grove-speech recognizer is Omni-directional.
This speech recognizer can recognize 22 commands including ‘start’, ‘stop’ and ‘Play music’. Every time it recognizes a command, it will return a value and the connected loudspeaker will repeat the command. This value can be used to control other devices like a motor or music player.
Note: The wake up word is “Hicell” (Pronounce it as one word). When it recognizes the awaken word the LED turns red and you can say the command word. If it recognize the command word, the LED will turn blue.
Note: The firmware of the module was wrote by the third party vendor, it’s not open source.
Application Ideas:
- Internet of Things
- Smart House
- Human Machine Interface
- Lighting Control
- Sensor Hub
- Robot
Features:
- Local Voice Recognition
- Very low rate of false triggering
- Speaker connector(JST2.0, speaker is not include)
- Built-in microphone
- 3.3/5V working voltage
- 22 recognition entry
- Default Baudrate: 9600
Tech specs
Specification
Item |
Min |
Typ |
Max |
Condition |
Operating Voltage |
3V |
3.3V |
5V |
25 ℃ |
Operating Current |
25mA |
26.5mA |
80mA@playing |
VCC = 3.3V 25℃ |
Operating Current |
25mA |
26.5mA |
130mA@playing |
VCC = 5V 25℃ |
Operating Temperature |
0℃ |
25℃ |
85℃ |
|
Size |
40*20mm |
|||
Weigth |
5g |
|||
Flash |
2Mbytes |
|||
Microphone Sensitivity |
-43dB |
-40dB |
-37dB |
VCC = 5V 25℃ |
Microphone SNR |
58dB |
|||
Microphone Directivity |
Omni-directional |
|||
Speaker Power |
1W |
VCC = 5V 25℃ |
||
Processor core |
Cortex-M0 |
|||
Processor Frequency |
32.768MHz |
50MHz |
VCC = 5V 25℃ |
Get Inspired
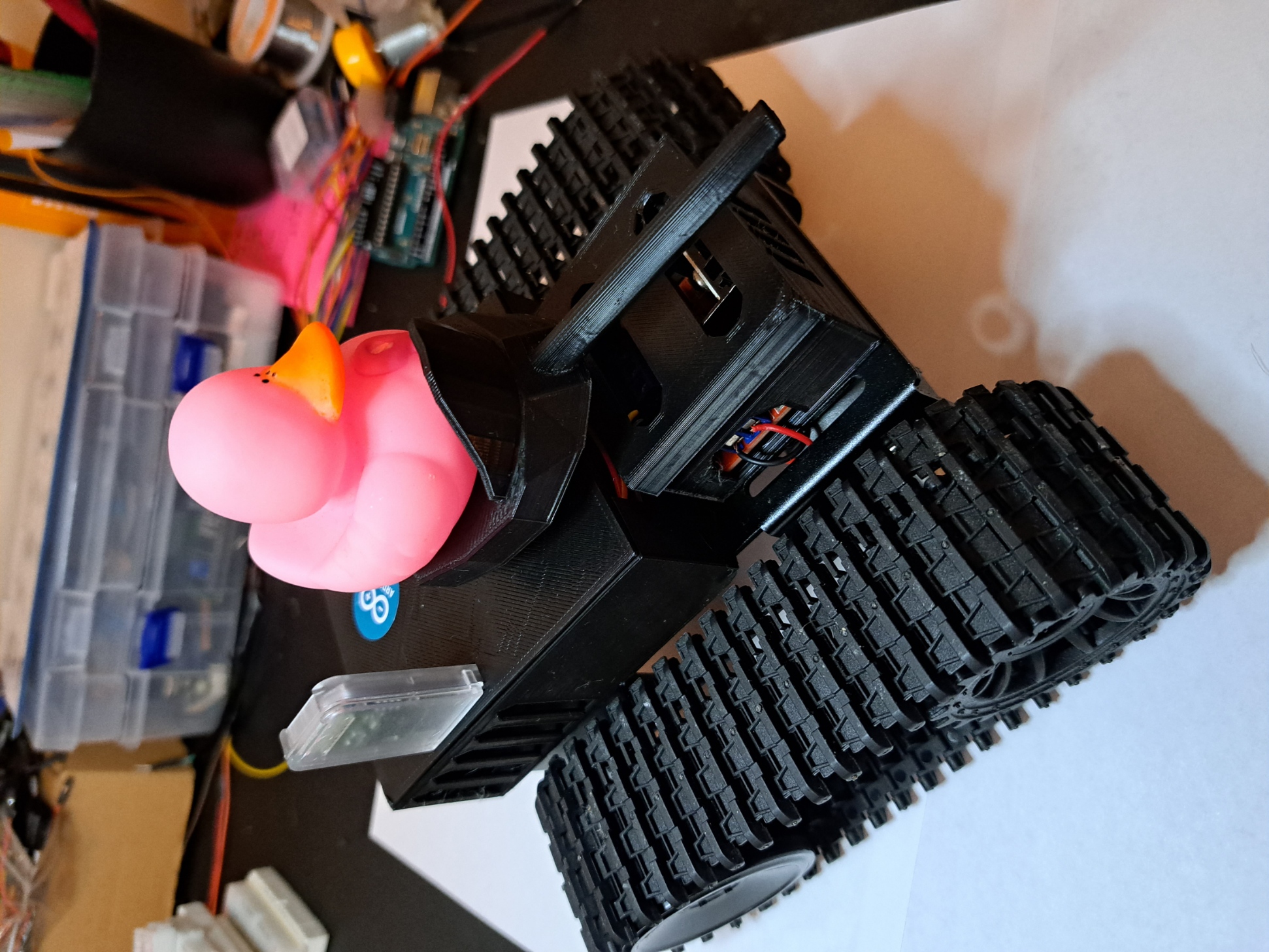
I'm excited to share the details of my BT Arduino Tank project, which incorporates some impressive 3D-printed components. While the main chassis of the tank was not 3D-printed, I utilized this technology to create two crucial parts: the enclosure for the motor driver and the compartment housing the remaining electronics. Additionally, I 3D-printed a cannon for an added touch of customization. The enclosure for the motor driver served as a protective housing, ensuring that the L298N motor driver module was securely mounted and shielded from external elements. By designing and 3D-printing this part, I could precisely fit it to the tank's specifications, providing a neat and organized arrangement of the electronics. In the same vein, the compartment for the remaining electronics, such as the Arduino Nano Every and the HC-05 Bluetooth module, was also 3D-printed. This enclosure offered a clean and organized solution for housing these components, safeguarding them while maintaining easy access for maintenance or modifications. Lastly, to enhance the tank's appearance and add a touch of personalization, I designed and 3D-printed a cannon. This custom-printed cannon perfectly complemented the overall design, making the tank even more visually appealing. By strategically incorporating 3D printing into specific parts of the project, I achieved a balance between functionality and customization. The precision and versatility of 3D printing allowed me to create tailored enclosures and a unique cannon, elevating the overall aesthetic and practicality of my BT Arduino Tank project.
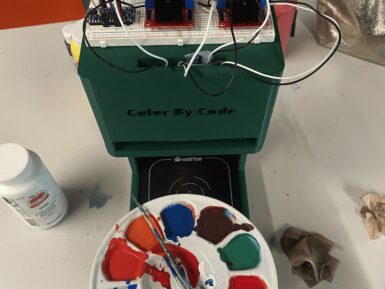
When you want to paint the walls in your bedroom that very specific shade of Misty Irish Green, all you have to do is head to your local hardware store and have them scan the corresponding card. The paint-mixing machine will then add the pigment to a white base and, a few minutes later, you have that exact color. So, shouldn’t you be able to do the same thing with acrylic paint for hobby purposes? Now you can, thanks to the “Color By Code” machine designed by Caltech students Frida Moreno and Asmat Kaur Taunque. Moreno and Taunque built Color By Code for a class project and it is, essentially, a hobby version of those hardware store paint-mixers intended for acrylic paint. As is the standard across many industries that deal with pigments, paint, and printing, this works using CMYK (cyan, magenta, yellow, key) color mixing. Here, the key is black and the machine takes an input color value for each component, then dispenses the paint in those ratios to achieve the desired hue. That all happens under the control of an Arduino Nano Every board. That operates peristaltic pumps, via L298N motor drivers, that dispense each color. Afterwards, a flushing procedure clears the lines before the next mix. The pumps fit into a 3D-printed stand, with the hoses dropping below to a waiting container. At this time, the user must set the color values through serial commands. But the team hopes to create a Bluetooth app in the future. They also plan to add a weight sensor, which would improve the machine’s accuracy.