
Overview
The Portenta Machine Control is a fully-centralized, low-power, industrial control unit able to drive equipment and machinery. It can be programmed using the Arduino framework or other embedded development platforms.
Thanks to its computing power, the Portenta Machine Control enables a wide range of predictive maintenance and AI use cases. It enables the collection of real-time data from the factory floor and supports the remote control of equipment, even from the cloud, when desired.
Key benefits include:
-
Shorter Time-To-Market
-
Give new life to existing products
-
Add connectivity for monitoring and control
-
Tailor it to your need, each I/O pin can be configured
-
Make equipment smarter to be ready for the AI revolution
-
Provide security and robustness from the ground up
-
Open new business model opportunity (e.g. servitization)
-
Interact with your equipment with advanced HMI
-
Modular Design for adaptation & upgrades
The Portenta Machine Control allows companies to enable new business-as-a-service models by monitoring customer usage of equipment for predictive maintenance and providing valuable production data.
The Portenta Machine Control enables industry standard soft-PLC control and is able to connect to a range of external sensors and actuators with isolated digital I/O, 4-20mA compatible analog I/O, 3 configurable temperature channels, and a dedicated I2C connector. Multiple choices are available for network connectivity, including USB, Ethernet, and WiFi/Bluetooth® Low Energy in addition to industry specific protocols such as RS485. All I/O are protected by resettable fuses and onboard power management has been engineered to ensure maximum reliability in harsh environments.
The Portenta Machine Control core runs a Portenta H7 microcontroller board (included), a highly reliable design operating at industrial temperature ranges (-40 °C to +85 °C) with a dual-core architecture that doesn’t require any external cooling. The main processor offers the possibility of connecting external Human Machine Interfaces like displays, touch panels, keyboards, joysticks, and mice to enable on-site reconfiguration of state machines and direct manipulation of processes.
The Portenta Machine Control’s design addresses a large variety of use scenarios. It is possible to configure a selection of the I/O pins via software. The Portenta Machine Control stands out as a powerful computer to unify and optimize production where one single type of hardware can serve all of your needs. Among other outstanding features are the following:
-
Industrial performance leveraging the power of Portenta boards
-
DIN bar compatible housing
-
Push-in terminals for fast connection
-
Compact device (170 x 90x 50 mm)
-
Reliable design, operating at industrial temperature rates (-40 °C to +85 °C) with a dual-core architecture that doesn’t require any external cooling
-
Embedded RTC (Real Time Clock) to ensure perfect synchronization of processes
-
Leverage the embedded connectivity without any external parts
-
CE, FCC, and RoHS certified
The Portenta Machine Control can be used in multiple industries, across a wide range of machine types, including: labelling machine, form & seal machine, cartoning machine, gluing machine, electric oven, industrial washer & dryers, mixers, etc.
Add the Portenta Machine Control to your existing processes effortlessly and become the owner of your solutions in the market of machines.
Tech specs
Processor |
STM32H747XI dual Cortex®-M7+M4 32 bit low power Arm® MCU (Portenta H7) |
Input |
|
Output |
|
Other I/O |
|
Communication Protocols |
|
Connectivity |
|
Memory |
|
Dimensions |
170 x 90 x 50 mm |
Weight |
186 gr |
Power |
24V DC +/- 20% |
Connector Type |
Push-in terminals for fast connection |
Operating Temperature |
-40° C to +85° C (-40° F to 185°F) |
Conformities
Resources for Safety and Products
Manufacturer Information
The production information includes the address and related details of the product manufacturer.
Arduino S.r.l.
Via Andrea Appiani, 25
Monza, MB, IT, 20900
https://www.arduino.cc/
Responsible Person in the EU
An EU-based economic operator who ensures the product's compliance with the required regulations.
Arduino S.r.l.
Via Andrea Appiani, 25
Monza, MB, IT, 20900
Phone: +39 0113157477
Email: support@arduino.cc
Documentation
Study how the Portenta Machine Control works using following files:
Portenta Machine Control schematics
SCHEMATICS IN .PDFPINOUT IN .PDFDATASHEET IN .PDF
Portenta H7 schematics
Learn more
Get Inspired
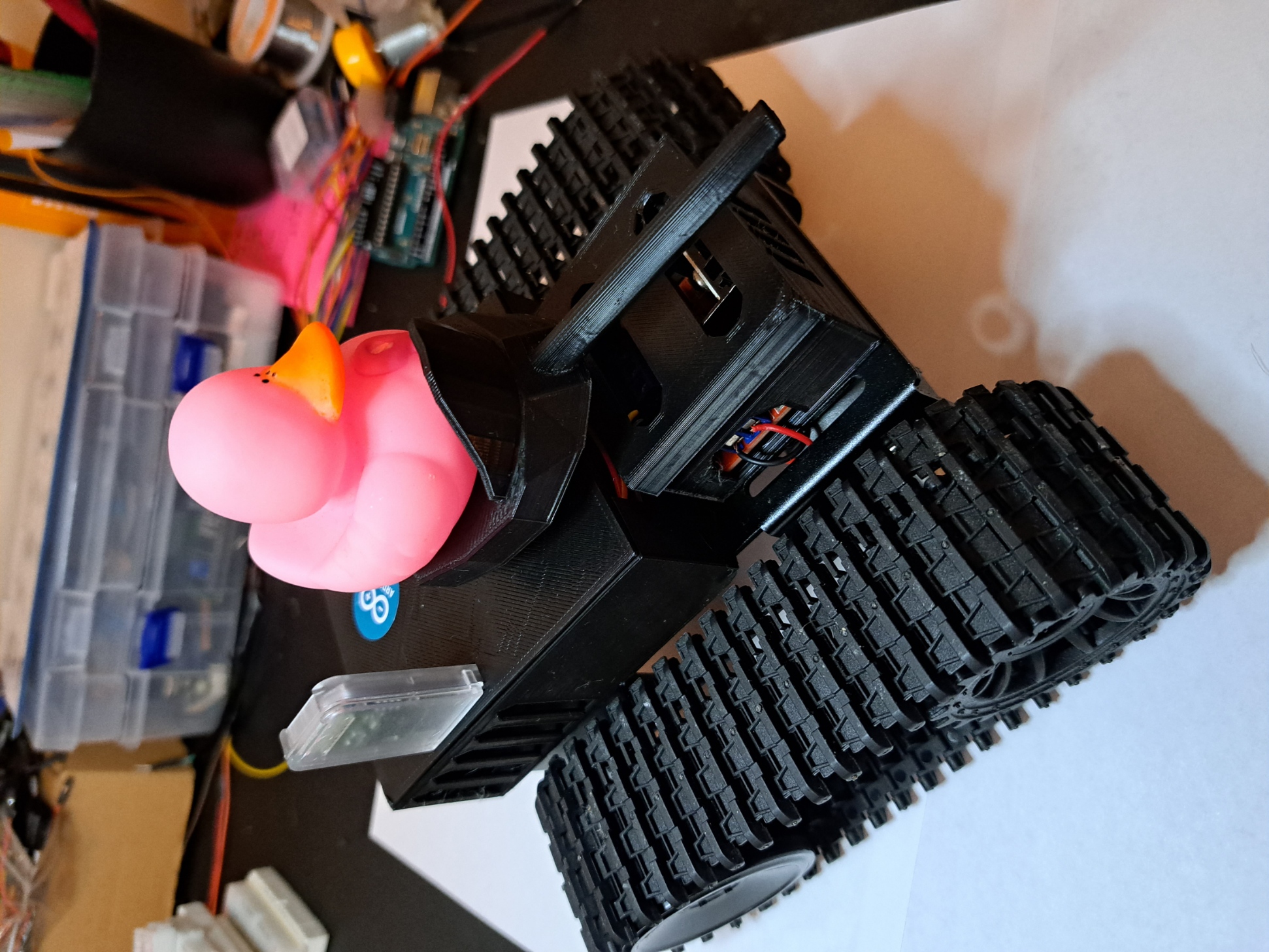
I'm excited to share the details of my BT Arduino Tank project, which incorporates some impressive 3D-printed components. While the main chassis of the tank was not 3D-printed, I utilized this technology to create two crucial parts: the enclosure for the motor driver and the compartment housing the remaining electronics. Additionally, I 3D-printed a cannon for an added touch of customization. The enclosure for the motor driver served as a protective housing, ensuring that the L298N motor driver module was securely mounted and shielded from external elements. By designing and 3D-printing this part, I could precisely fit it to the tank's specifications, providing a neat and organized arrangement of the electronics. In the same vein, the compartment for the remaining electronics, such as the Arduino Nano Every and the HC-05 Bluetooth module, was also 3D-printed. This enclosure offered a clean and organized solution for housing these components, safeguarding them while maintaining easy access for maintenance or modifications. Lastly, to enhance the tank's appearance and add a touch of personalization, I designed and 3D-printed a cannon. This custom-printed cannon perfectly complemented the overall design, making the tank even more visually appealing. By strategically incorporating 3D printing into specific parts of the project, I achieved a balance between functionality and customization. The precision and versatility of 3D printing allowed me to create tailored enclosures and a unique cannon, elevating the overall aesthetic and practicality of my BT Arduino Tank project.
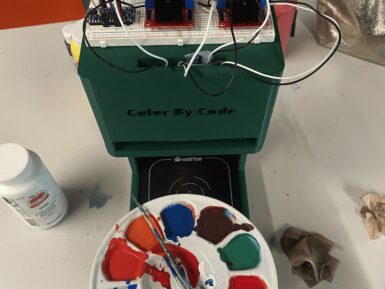
When you want to paint the walls in your bedroom that very specific shade of Misty Irish Green, all you have to do is head to your local hardware store and have them scan the corresponding card. The paint-mixing machine will then add the pigment to a white base and, a few minutes later, you have that exact color. So, shouldn’t you be able to do the same thing with acrylic paint for hobby purposes? Now you can, thanks to the “Color By Code” machine designed by Caltech students Frida Moreno and Asmat Kaur Taunque. Moreno and Taunque built Color By Code for a class project and it is, essentially, a hobby version of those hardware store paint-mixers intended for acrylic paint. As is the standard across many industries that deal with pigments, paint, and printing, this works using CMYK (cyan, magenta, yellow, key) color mixing. Here, the key is black and the machine takes an input color value for each component, then dispenses the paint in those ratios to achieve the desired hue. That all happens under the control of an Arduino Nano Every board. That operates peristaltic pumps, via L298N motor drivers, that dispense each color. Afterwards, a flushing procedure clears the lines before the next mix. The pumps fit into a 3D-printed stand, with the hoses dropping below to a waiting container. At this time, the user must set the color values through serial commands. But the team hopes to create a Bluetooth app in the future. They also plan to add a weight sensor, which would improve the machine’s accuracy.