
Arduino Edge Control
A remote monitoring and control solution, optimized for outdoor environments.
Collect real-time data from smart sensors and leverage AI on the edge.
Overview
It can be positioned anywhere and is suitable for precision farming, smart agriculture, and other applications requiring intelligent control in remote locations. Power can be either supplied via solar panel or DC input.
Remotely control your application through the Arduino Cloud (or third-party services) using a choice of connectivity options suitable to the location. The Arduino Edge Control features built-in Bluetooth® and its connectivity can be expanded with 2G/3G/CatM1/NB-IoT modems, LoRa®, Sigfox, and WiFi by adding anyone of the MKR boards.
The Arduino Edge Control is capable of connecting sensors and drive actuators like latching valves (common in agriculture). Moreover, it has the capability to provide real-time monitoring over the entire process, thereby reducing production-related risks.
Particularly suited to smart agriculture, the sensors can collect real-time data such as weather conditions, soil quality, crop growth, amongst others. Once sent to the Arduino Cloud, the data value chain becomes valuable analytics that supports business processes at various levels (e.g. crop yield, equipment efficiency, staff performance, etc.). The Arduino Edge Control has the capability to improve crop quality and reduce human effort/error by automating processes like irrigation, fertilization, or pest control.
Application Examples
- Automated Greenhouses
Automatically manage the humidity and temperature to ensure the best environment for crop growth, minimising carbon emissions and increasing economic yield. The inclusion of an Arduino MKR GPS Shield allows for optimum crop rotation planning and acquisition of geospatial data.
- Hydroponics/Aquaponics
Since hydroponics involves the growth of plants without soil, delicate care must be taken to maintain the conditions required for optimum growth. The Arduino Edge Control can be set-up to control these conditions with minimal manual labour.
The Arduino Edge Control can help match the even higher requirements of Aquaponics, by providing automated control over the internal process and reducing production risks.
- Mushroom Cultivation
Mushrooms are notorious for requiring the perfect temperature and humidity conditions to sustain spore growth, while also preventing competing fungi from growing. Thanks to the numerous watermark sensors, output ports and connectivity options available on the Arduino Edge Control, this precision farming can be achieved on an unprecedented level.
Tech specs
Microcontroller | nRF52840 (64 MHz Arm® Cortex-M4F) |
Digital Input | 6x edge sensitive wake up pins |
Digital Output | 8x latching relay command outputs with drivers 8x latching relay command outputs without drivers |
Relays | 4x 60V/2.5A galvanically isolated solid state relays |
Analog Input | 4x 4-20mA inputs 8x 0-5V analog inputs 16x hydrostatic watermark sensor input |
Terminal Block Connectors | 6x 18 pin plug in terminal block connectors |
Power Supply | 12 V Acid/lead SLA Battery Supply (Recharged via solar panels) |
Power Consumption | Low power (up to 34 months on a 12V/5Ah battery) 200uA Sleep current |
Memory | 1 MB onboard Flash memory 2 MB onboard QSPI Flash memory |
SD Card | Interface for SD Card connector (through expansion port only) |
Connectivity |
Bluetooth |
Peripherals | Full-speed 12 Mbps USB Arm CryptoCell CC310 security subsystem QSPI/SPI/TWI/I²S/PDM/QDEC High speed 32 MHz SPI Quad SPI interface 32 MHz 12-bit 200 ksps ADC 128 bit AES/ECB/CCM/AAR co-processor |
Operational Temperature | -40° C to +85° C (-40° F to 185°F) |
Length | 104 mm |
Width | 86 mm |
Conformities
Resources for Safety and Products
Manufacturer Information
The production information includes the address and related details of the product manufacturer.
Arduino S.r.l.
Via Andrea Appiani, 25
Monza, MB, IT, 20900
https://www.arduino.cc/
Responsible Person in the EU
An EU-based economic operator who ensures the product's compliance with the required regulations.
Arduino S.r.l.
Via Andrea Appiani, 25
Monza, MB, IT, 20900
Phone: +39 0113157477
Email: support@arduino.cc
Documentation
Study how the Arduino Edge Controls works using following files:
SCHEMATICS IN .PDF DATASHEET IN .PDF
Pinout Diagram
Download the full pinout diagram as PDF here.
Learn more
Get Inspired
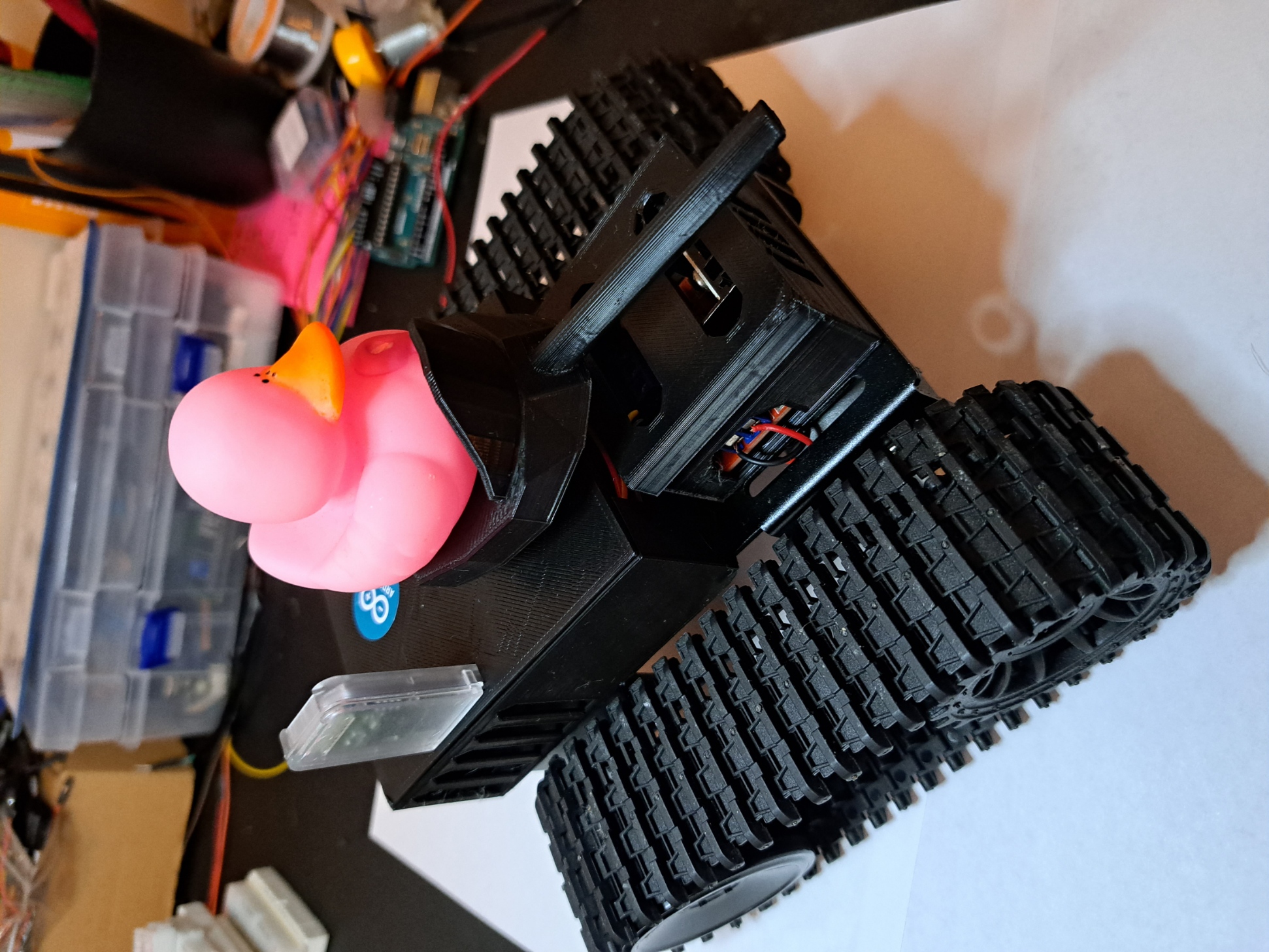
I'm excited to share the details of my BT Arduino Tank project, which incorporates some impressive 3D-printed components. While the main chassis of the tank was not 3D-printed, I utilized this technology to create two crucial parts: the enclosure for the motor driver and the compartment housing the remaining electronics. Additionally, I 3D-printed a cannon for an added touch of customization. The enclosure for the motor driver served as a protective housing, ensuring that the L298N motor driver module was securely mounted and shielded from external elements. By designing and 3D-printing this part, I could precisely fit it to the tank's specifications, providing a neat and organized arrangement of the electronics. In the same vein, the compartment for the remaining electronics, such as the Arduino Nano Every and the HC-05 Bluetooth module, was also 3D-printed. This enclosure offered a clean and organized solution for housing these components, safeguarding them while maintaining easy access for maintenance or modifications. Lastly, to enhance the tank's appearance and add a touch of personalization, I designed and 3D-printed a cannon. This custom-printed cannon perfectly complemented the overall design, making the tank even more visually appealing. By strategically incorporating 3D printing into specific parts of the project, I achieved a balance between functionality and customization. The precision and versatility of 3D printing allowed me to create tailored enclosures and a unique cannon, elevating the overall aesthetic and practicality of my BT Arduino Tank project.
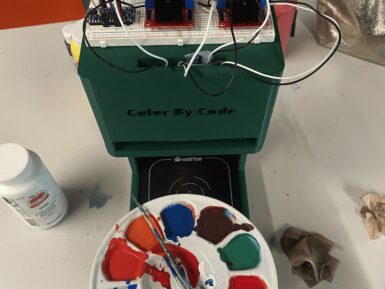
When you want to paint the walls in your bedroom that very specific shade of Misty Irish Green, all you have to do is head to your local hardware store and have them scan the corresponding card. The paint-mixing machine will then add the pigment to a white base and, a few minutes later, you have that exact color. So, shouldn’t you be able to do the same thing with acrylic paint for hobby purposes? Now you can, thanks to the “Color By Code” machine designed by Caltech students Frida Moreno and Asmat Kaur Taunque. Moreno and Taunque built Color By Code for a class project and it is, essentially, a hobby version of those hardware store paint-mixers intended for acrylic paint. As is the standard across many industries that deal with pigments, paint, and printing, this works using CMYK (cyan, magenta, yellow, key) color mixing. Here, the key is black and the machine takes an input color value for each component, then dispenses the paint in those ratios to achieve the desired hue. That all happens under the control of an Arduino Nano Every board. That operates peristaltic pumps, via L298N motor drivers, that dispense each color. Afterwards, a flushing procedure clears the lines before the next mix. The pumps fit into a 3D-printed stand, with the hoses dropping below to a waiting container. At this time, the user must set the color values through serial commands. But the team hopes to create a Bluetooth app in the future. They also plan to add a weight sensor, which would improve the machine’s accuracy.